JCB digging deep to rid the roads of pothole misery
The billionaire businessman Lord Bamford has a keen interest in the state of Britain’s roads. The boss of JCB, who was born in Staffordshire, spends long hours travelling along the highways and byways of the UK.
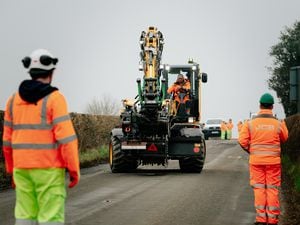
Like so many motorists, he was acutely aware of the poor state of Britain’s roads. So he tasked workers at his company to find a solution; to create a low-cost, efficient and expedient way of fixing potholes.
It took more than a year for JCB workers to create, test and sign off a revolutionary product – the PotHole Pro – but now that it’s on the market they are set to transform the nation’s roads.
The product will provide employment for local workers, help local councils to save millions of pounds in maintenance costs while also dramatically improving the state of British roads.
After being sent to market earlier this year, the PotHole Pro has already secured huge interest from local authorities around the UK, who see it as the solution to many of their highways problems.
Ben Rawding, from JCB’s Product Team, worked on the PotHole Pro. He takes up the story. “This project was very much about researching the issue of potholes and trying to understand the difficulties in repairing them.
“We’re all in the same position with our roads and so many people wanted to know why we have a problem with potholes and why it takes so long for councils to repair them.”
JCB started off with a simple question: what did the process of repair look like? Once they’d answered that, they examined whether they could speed up the process, while also making savings on cost.
“It was about breaking down the process and then designing the machine.
“It was led by our chairman, Lord Bamford, who is passionate about the UK network. He genuinely wanted to help.”
Roads in Staffordshire and Shropshire were at the forefront of minds at JCB as they set to work. Prototypes were used locally, cleaning out roads and filling in potholes to see whether Lord Bamford’s brainwave would work. Thankfully, it did.
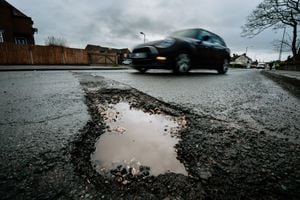
Ben says: “Lord Bamford is a motorist too so he sees the problem.
“We all have our own stories of people who are affected by this. There’s a big health and safety issue for the likes of cyclists and motorcyclists and we are all aware of people who’ve been seriously injured or, in some cases, where fatalities have occurred.
“There is frequent damage to vehicles, which has a significant cost, and then there’s the environment and the economy to consider. Fixing potholes usually involves several machines and the cost can be very high.”
One of the key issues in JCB’s programme was to establish a permanent repair.
Councils around the UK often patch up roads, only to see them rapidly degrade and for potholes to re-appear. Lord Bamford’s brief was that the company should find something more permanent, that they should banish the days of the patch-up and create a machine that would provide a lasting solution.
Ben, a post-graduate from De Montford University, in Leicester, joined JCB as a commercial and technical sales graduate. He was pleased to get his teeth into the project, along with experienced colleagues.
The brief wasn’t simply to solve the perennial problem of potholes. It was also to save money and drive down the cost of repair while helping to tackle the thorny issue of industrial injury.
Fixing potholes doesn’t just cost money, it also costs lives. There have been too many fatalities as workmen maintain a position in live carriageways, while an equally insidious problem has been the number of workmen who’ve suffered industrial injuries.
Ben explains: “There’s a big problem in terms of fixing Britain’s road and it’s all about how we go about it. We wanted to do a permanent repair. There’s not much point authorities doing these temporary repairs, it’s a numbers game so that authorities can show they’re active but the repairs last a month so it genuinely is pointless.
“It doesn’t make sense to visit every month or so. It has to be a permanent repair.
“Then there’s big health and safety message. At the moment, we have highways operators using jack hammers or circular saws and they are operating in live carriageways. That’s just not safe. So moving away from that system to one where we have a machine operated in a raised cabin, a safe distance from the road, also has a profound effect.”
Simply, it gets guys out of the road and removes the risk to life. But there’s more.
“The cabin provides protection for the machine operator. But it also helps to solve the problem of something known in the trade as ‘white finger’.”
White finger is the injury that arises from persistent use of a vibrating power tool. It literally damages the connective tissue in the arms and joints of the machine operators.
“There are guys who’ve suffered so much white finger that they can no longer pick the machines up. They’ve done so much damage to their hands and wrists and arms that they’re living with a permanent industrial injury.
“That’s a huge issue. It’s something called hand-arm vibration syndrome. It’s a key priority in the industry.
“Councils are facing huge numbers of claims from people who’ve been injured in that way, while people who’ve suffered are also living with that acquired disability.
“So our objective was to make pothole repair safer, quicker, more cost-effective and more efficient.
“We didn’t want a system where Mr Motorist was navigating around guys in the motorway who were damaging themselves by fixing holes on a temporary basis.” Which is what happens now.
The results of JCB’s research and development were remarkable. They created a device that has the ability to fix a pothole in just eight minutes.
That means there’s less disruption for motorists – as well as all of the other benefits – so the wheels of industry can continue to turn and so motorists don’t face lengthy delays on their way to work.
“We tried to distill three key methods: cutting, cropping and cleaning. We went back to the drawing board and asked ourselves ‘what’s the process?’ What do we want to achieve?”
The answer was the three C’s – cutting the road surface, cropping it into a neat square and then cleaning out the new cavity so that it can be filled.
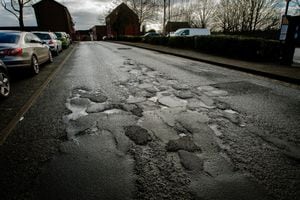
Ben says: “If we use the analogy of a dentist. A dentist has to remove all of the decayed material, rather than just fill a gap in someone’s tooth. That’s what we try to do.
“We cut the tarmac, take away the damaged material, then we crop it by squaring off the edges; it has to be nice uniform square edges which help to make it a permanent repair.
“You have to have a solid structure for new material to bind onto, it’s no good having a wavy line because the repair will quickly degrade as people drive over it and as the weather takes effect.”
After the square hole is cut, it has to be cleaned with the milled tarmac being moved out of the way. “The key challenge faced by authorities is the preparation, it’s not the reinstatement.
“The preparation can takes hours at a time. At the moment, authorities are using vibrating tools and also using large road machines, like planers, which are really expensive. So councils are facing huge costs, they’re hitting large numbers every day.”
JCB’s priority was to simplify, drive down costs and make it more efficient.
“The other day, we fixed 56 potholes in one day. That’s just one day’s work. A council might fix eight in a day, using a two-man reactive team and manual technology, with vibrating tools. Councils are using the same technology that was used 25 years ago but it’s no longer fit for purpose.
“Currently, the best a council can operate at is one pothole every 45 to 60 minutes. We’ve got that down to eight and made it safer, better and cheaper.”
All of which is great news for the tax payer. Where budgets had previously been £50-£60 per hole, it’s been driven down to around £30. That means money is left over as savings or to be reallocated into other pots of our local council’s hard-hit finances.
The only part of the process that hasn’t changed is the reinstatement. Adding tar and pounding it into the square hole remains the endgame in the process.
The proof of the pudding, of course, is in the eating and the feedback from road users has been impressive.
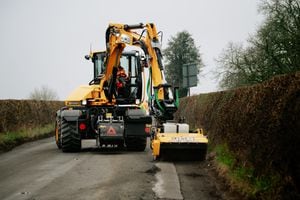
While councils like the savings, the absence of industrial injury and the speed with which repairs take place, the motorists like the fact they’re driving over a road that is permanently fixed, rather than one which crumbles within a few months.
Ben adds: “In Shropshire, I had a gentleman write into me. I think he’d seen a road and he wanted to complain about the quality of repairs. He wrongly thought that we’d been the crew that had fixed it using the Pothole Pro. So he wrote a letter narrating the poor quality of repairs.
“I checked on the pothole to see who’d fixed it. It turns out he was complaining about repairs that had been manually by traditional gangs; the repairs we’d done were fine. It all comes back to the same old issue. Councils feel compelled to do temporary repairs and they just don’t work.”
The process of creating Pothole Pro took just over a year. The machine has been designed so that it can manage small potholes, so that it can effect repairs before a small problem becomes a big one. Elsewhere, it can sheer off whole sections of road and do far, far larger sections of tarmac. The key, of course, is that it’s uniform.
It doesn’t matter if the workmen are having a bad day, suffering from white finger or want to get home because it’s raining. The machine carries out the same repair day after day after day.
“It took just over a year. It was all about refining the process. It was about working through the detail, staying focused and concentrating on our key priorities.
“We wanted to do the testing in real world environments, on roads that people use. So we needed to be sure it worked in the street, on different types of road surface, in areas where there were overhead cables and without adding to delays or costs. We’ve done that. the validation is now complete and the response to our proposition from our customers has been amazing.
“We’ve been out to see 50 local authorities, from the Highlands of Scotland to Central London or to the busy M6. We’ve fixed 16,500 potholes in three months but most local authorities usually do 10,000 in a year.
“Councils are telling us the PotHole Pro is a no-brainer. The other process is slower and more costly with older tech.”
And so to business.
Some authorities will buy the PotHole Pro as a one-off purchase, others, like Shropshire, use such contractors as Kier who carry out their repairs.
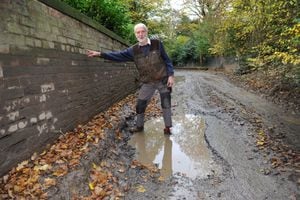
The vision of Lord Bamford is being realised. The industrialist and entrepreneur who spotted a problem and led a team to fix it is achieving his aim.
Ben says: “I hope Lord Bamford will be pleased, though the proof is in the pudding. The potholes are being fixed and the machine is being debated in the House of Commons. It’s turned a lot of heads.
“We had a big product team. It literally involved hundreds of people across JCB who all played a small part.
“We are all very, very passionate about fixing the problem. This is the latest and greatest innovation that will make a huge difference.”
There’s only one more question: cost. The PotHole Pro is undoubtedly a quantum leap – but is it one that’s affordable?
It’s a simple answer: yes. Prices start from around £619 per week for an operating lease – and that’s against a backdrop of an industry where a pothole in the UK is fixed every 19 seconds at a cost of £60.
PotHole Pro halves the cost – a planer, for instance, can cost £900 per day to hire.
Better roads, fewer council tax demands and less injuries to workmen – what’s not to like?