Liquidators called in to wind up Telford company that made PPE during pandemic
A 60-year-old company that made protective equipment during the pandemic has appointed liquidators to wind up the business.
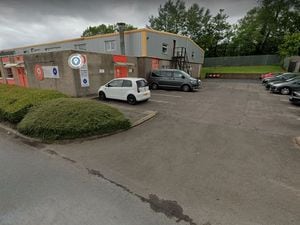
Ambroplastics Limited, based at Chamber House, Halesfield 13, in Telford, was voluntarily wound up by company director Phil Caudle at a general meeting of the members of the company.
An official record of the meeting in Birmingham on December 21 was told: "That it has been proved to the satisfaction of the undersigned Phil Caudle, director that the company cannot, by reason of its liabilities, continue its business and accordingly that the company be wound up voluntarily."
It is officially known as a creditors` voluntary liquidation, and joint liquidators Timothy Higgins and Edward Williams of PricewaterhouseCoopers LLP have been appointed to liquidate the business. At one point during the pandemic, the company had employed 23 people.
Ambroplastics was incorporated as a business in 1962 and was a UK-based manufacturer of presentation products, specialising in polypropylene.
During the pandemic the company was praised for pivoting its business to make protective face visors for key workers and other personal protective equipment (PPE).
According to a report in the Shropshire Star it had despatched more than 700,000 units, with orders for another million to complete.
Phil Caudle, managing director of the firm, said at the time: “2020 had been tough so far and the coronavirus situation was not welcome from an economic point of view. The face masks have thrown us a much-needed lifeline and it is 90 per cent of what we are doing currently.
“We had joked about them when news was first breaking about the virus. I asked our CAD guy to design one as the basic principle of the manufacture of the parts – a strap and a visor. It is effectively what we do everyday and we can manufacture at volume. We can punch out around 90,000 units in a normal working day and of course increase this if we had to.
“We are not a company that work shifts in the main, but if the need arose we would find a way. The main issue for everyone is the availability of raw materials and we are fortunate that our suppliers have risen to the challenge and the call for help.
“We are supplying to our existing customers who have contacts with NHS trusts. We supply medical files to these businesses already, so we are relying on a trade customers to get these into the relevant trusts as well as contacting the PPE Exchange, and other contacts to provide assistance where we are able. We have donated 500 units to the Nightingale in Birmingham via a customer who is volunteering there.”
Google reviews at the time praised the company for its "outstanding innovation, quality and customer service," "good people making masks" and for being a "forward thinking company working for the good of everyone."